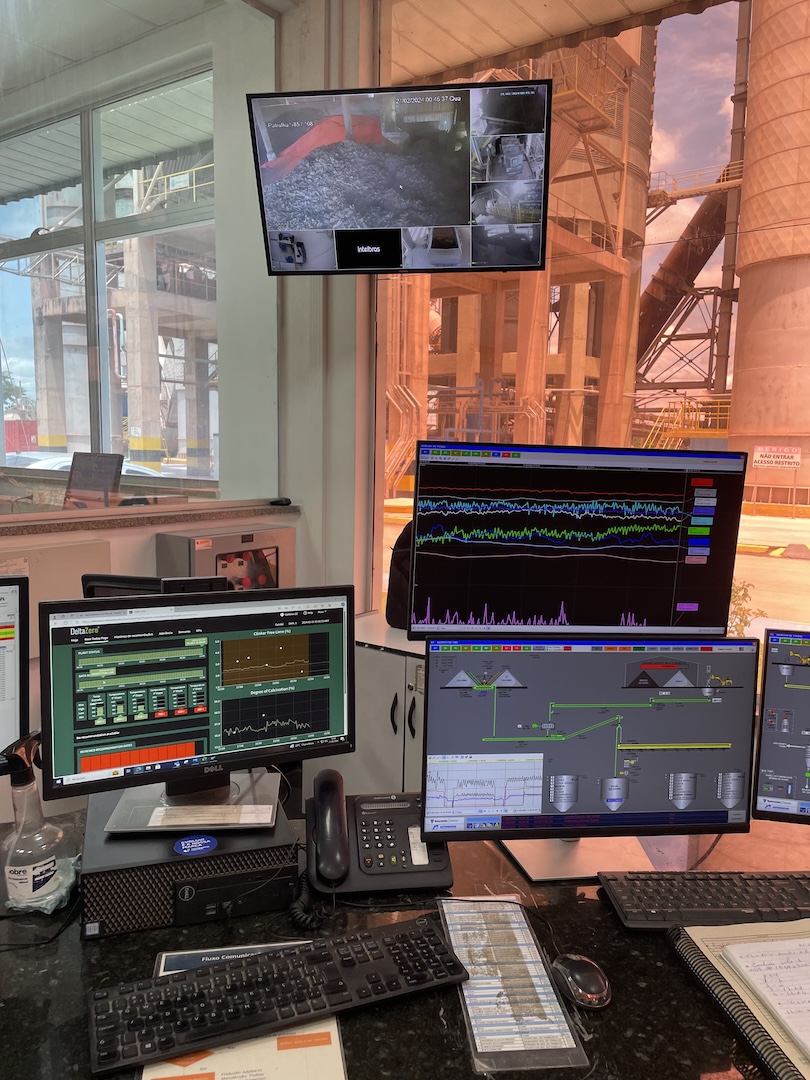
Historically, cement plants have utilised fossil fuels as their primary fuel source. This high dependence on coal has been driven by its availability, energy density, and cost-effectiveness. However, as environmental regulations tighten and pressure to meet sustainability goals is growing, the industry has been pushed to explore and adopt alternative fuels to reduce the environmental footprint of cement production. But with this increased use of alternative fuels new complications emerge, notably in the form of buildups within cyclones and kilns. These buildups can impede airflow and material movement, leading to decreased efficiency and potential shutdowns. This article explores the origins of these buildups, assesses their impact on plant operations, and examines how artificial intelligence (AI) can play a pivotal role in mitigating these challenges and enhancing overall efficiency.
The origin of buildups and the role of alternative fuels
Buildups in cement plants, such as blockages and ring formations, predominantly occur in the preheater tower and kiln. These blockages and rings result from the solidification of raw meal or fuel ash under high-temperature conditions. The fine particles agglomerate and gradually form larger masses that adhere to equipment surfaces.
Alternative fuels generally have more complex chemical and physical properties than traditional fuels, such as higher levels of chloride and sulphur or lower ash melting points. These characteristics can lead to more frequent and severe blockages and ring formations within the equipment. Chloride is particularly worrisome, it condenses at around 800°C, forming sticky liquid layers in the preheater tower which facilitates the accumulation of particles, further intensifying blockages and ring formations. What’s more, when alternative fuels do not burn completely or uniformly, the risk of material buildup increases, potentially leading to operational disruptions and efficiency losses.
While beneficial for the environment, alternative fuels introduce a significant level of complexity to the cement production process that, if not addressed, can lead to severe operational inefficiencies, reduced clinker quality and negative environmental impact.
To effectively manage these challenges, cement plants rely on analytical tools like the image below. This is a common tool for assessing blockage risks in cement plants, illustrating the interaction between chlorine and sulphur. By evaluating these dynamics, operators can gauge the amount of volatiles in their system and take measures to avoid disruptions, enhancing operational efficiency and sustainability. Chlorine and sulphur levels are measured from hot meal samples, which are typically taken at a lower frequency (typically every 2-4 hours), necessitating a careful approach to data collection and analysis to maintain continuous and effective monitoring.
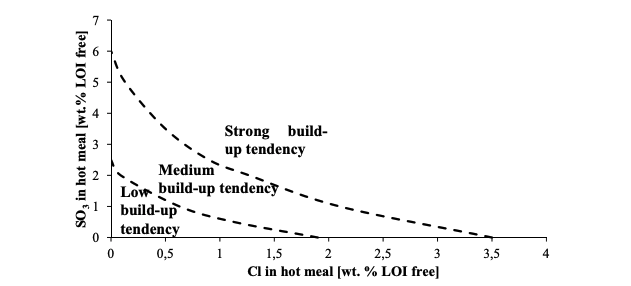
Figure 1: Evaluation diagram of build-ups tendency as a function of SO3 and Cl content in hot meal from Review: Circulation of Inorganic Elements in Combustion of Alternative Fuels in Cement Plants.
Leveraging AI for operational excellence
Monitoring Key Parameters with AI
Advancements in AI are transforming how cement plants monitor critical operational parameters that influence buildups. Currently, the processes plants have to detect blockages, such as measuring the levels of chlorine and sulphur, can only identify the increasing likelihood of an issue rather than actually predicting when a blockage will happen.
By integrating AI with real-time data from pressure, temperature sensors, and gas analyser data, Carbon Re can identify anomalies that precede a ring formation or blockage, giving operators time to proactively adjust processes to prevent unplanned outages or minimise the severity of the build-up event. This not only prevents potential blockages but also ensures the plant operates within optimal parameters, thereby reducing maintenance downtime and improving overall efficiency. The following figure illustrates how AI can utilise high-resolution data to detect spikes in temperature and pressure that precede a shutdown caused by a blockage. By tracking these key features, data-driven methods can identify anomalies and proactively adjust processes to maintain stable operations and prevent unplanned outages.
AI algorithms can optimise fuel mixing and feeding strategies, ensuring more complete combustion and reducing the likelihood of buildups. Machine learning models can continually adjust operational parameters based on the incoming data on fuel characteristics and operational conditions, thus maintaining optimal combustion conditions and minimising the formation of blockages.
Enhancing process control
Advanced control systems powered by AI can monitor various process variables and dynamically adjust the process, balancing the operation and reducing the risk of buildup. For instance, AI can optimise the air-to-fuel ratio, kiln speed, and temperature profiles within the kiln to ensure efficient operation while minimising the risk of material deposits. Additionally, these AI-driven systems enhance the plant’s ability to safely increase the use of alternative fuels by detecting volatile components. By proactively making adjustments based on these detections, plants can increase its Thermal Substitution Rate (TSR), thereby reducing reliance on traditional fuels.
The integration of AI into cement plant operations offers a promising avenue to tackle the longstanding issue of buildups, especially as plants shift towards the use of more sustainable but challenging alternative fuels. By leveraging AI for data utilisation, process optimisation, and enhanced control, cement plants can not only reduce the frequency and impact of buildups but also achieve greater operational efficiency and sustainability. As we continue to advance in our digital capabilities, the potential to transform these traditional industrial environments grows, leading to a smarter, more efficient future in cement production.