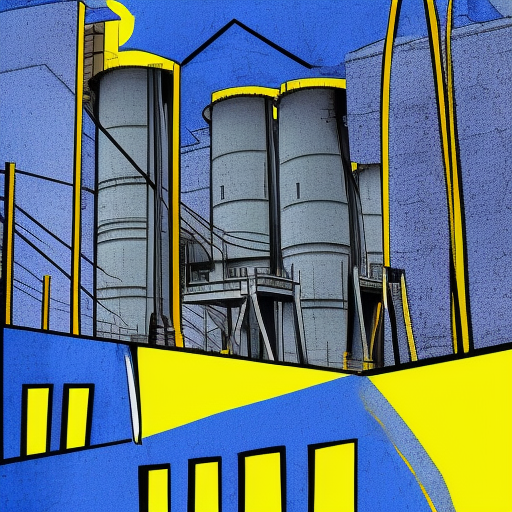
The digital age, marked by data utilisation and advancements in AI, is transforming our lives. In the cement industry, this transformation is still emerging, with over 60% of plants yet to embark on any digital initiatives. However, the efficiency, profitability, and sustainability benefits of AI are becoming too significant for cement companies to overlook, prompting many to assess their AI readiness. Below, we detail some of the key considerations for cement producers to help determine when to add AI to their technology suite.
Ideal plant conditions
As with any project, AI implementation requires the support of the onsite teams to manage upgrade and maintenance schedules. Producers should plan their AI deployment around plant upgrades, aiming for a six-month period without scheduled upgrades and minimal maintenance issues. It is crucial that the plant maintains steady-state conditions, either through an expert system or manual operation, for the production stage where AI will be used, such as the pyroprocess. For AI solutions providing closed-loop control, like our AI-powered pyroprocess control solution, existing automation technology must already be in place.
Technological readiness
Data collection and utilisation form the foundation of AI optimisation. Thanks to Industry 4.0 initiatives, cement plant operations generate extensive data from installed sensors, measuring crucial variables such as fuel flows, temperatures, pressures, atmospheric conditions, mechanical speeds, electricity consumption, chemical analysis, and quality data. These variables are sampled at various time resolutions, ranging from 500 milliseconds to hourly or daily intervals.
In order to ensure AI readiness, cement plants need to collect and store all process data signals, with lab measurements and process data accessible through the same data management system. Plants should ensure that they have collected historical data – at least 6 months’ worth – before initiating AI optimisation model development, as this is crucial to train and improve models.
Cloud-based solutions are preferred to the traditional ‘on-prem’ for AI optimisation as cloud solutions offer flexibility, enabling remote access to centralised data and applications from anywhere with an internet connection. Additionally, cloud users can access a variety of powerful services without requiring intricate integration projects or extensive hardware investments and the need for onsite infrastructure maintenance and updates is also eliminated.
The final piece of the puzzle is data utilisation. AI can provide unique and novel insights into the cement production process. However, if these insights are not then fully utilised, the impact on bottom-line performance will be diminished. One way to use this new information is to input the AI predictions and recommendations into an existing expert system. Allowing for the frequency of updates and speed of response to be greater than can be handled by a human operator. AI systems are not constrained to plants with Expert Systems and can also offer considerable value to a manually operated process. However, In this case, a strong culture of change management and a willingness to embrace the new technology is necessary to maximise the benefits of the system.
Strategic priorities required
Digitalisation is a competitive advantage for cement companies and must be seen as a strategic priority. Companies need to set realistic yet ambitious targets that outline the vision, value, and key priorities at the company and site levels. Cement companies are faced with competing challenges – increasing costs, the need to maintain throughput and environmental priorities, those with a desire to adapt through the use of the most innovative technologies will come out on top. Focusing on AI readiness, cement companies’ digitalisation roadmaps should encompass not only investment strategies—studies indicate that success in digitalisation programs correlates with investment—but also people and culture management, and the adoption of data standards.
An effective change management programme, where a culture of innovation and employee engagement in AI is cultivated, is the most critical component for successful digital transformation – notably, 70% of all of the World Economic Forum’s Global Lighthouse Network recognise this. Producers must ensure their strategy includes a talent roadmap that prioritises upskilling incentives and opportunities so that employees can understand and operate AI-powered systems effectively. Companies must also recognise that AI projects will need ongoing support to ensure success – AI for pyroprocess control may require input from process engineers at the plant as well as a centralised Industry 4.0 lead to work with AI providers.
The adoption of data standards is key for companies to realise the potential of their abundant data and ensure structured, accessible, interoperable, and coherent data across their plants. In our whitepaper, Digitalisation: The Pathway to Net Zero, we highlight how producers can use the FAIR principles to facilitate data-driven decision-making.
Although there’s no one‐size‐fits‐all method for AI success, producers who understand their AI readiness and plan the timing of their AI implementation to maximise success will come out on top. For many producers, the foundations are already in place, and the next step is simply engaging with an AI provider to assess the opportunity.
Unlock the benefits of AI
Carbon Re is working with plants across the globe to reduce fuel consumption and carbon emissions while increasing plant stability and product quality.
Get in touch to see how we can help your plant.