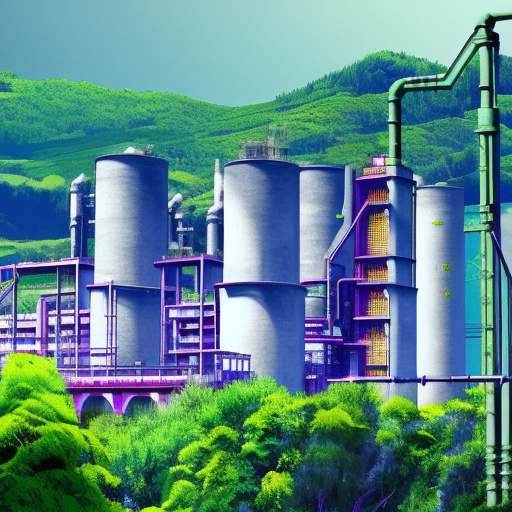
Decarbonising the production of cement is essential for addressing the climate crisis and for securing the future of the industry. As the biggest source of industrial greenhouse gas emissions, and a vital construction material that forms the foundation of modern infrastructure, the sustainable transformation of cement production is crucial.
Cement companies recognise this challenge and welcome the opportunity to innovate to improve their sustainability outcomes. However, cement producers expect limited progress in emissions reductions before 2030. More than any other industrial sector, we are seeing a widely accepted reliance on Carbon Capture and Storage (CCS) technologies as the only viable route to decarbonising the industry, but CCS is not expected to be implemented at scale before 2040–2050.
The ‘time value of carbon’ which underpins the urgent need for emissions reduction by 2030, is an important concept that is often overlooked. The greenhouse gases emitted today have longer in the atmosphere to cause harm than gases emitted in the future – this means that the biggest impact we can have on the future temperature of our planet is through emissions that we reduce now. This is supported by research published in Nature in 2021, which shows achieving large emissions reductions by 2030, without ever reaching net zero, delivers a significantly better result than reaching net zero through a big improvement between 2040 and 2050.
Given the increasing urgency of the climate crisis, cement producers cannot afford to wait for emerging technologies like CCS. They must adopt available technologies and policy levers to reduce emissions immediately. The World Benchmarking Alliance’s Climate and Energy Benchmark recently reported that the emissions intensities of heavy industry companies, including cement, are not aligned with the 1.5°C carbon reduction strategy and this is primarily due to a lack of investment in market-ready technologies.
Luckily for cement companies, the benefits enabled by digitalisation and next-generation measurement devices could reduce emissions in the cement industry by an estimated 10%, and the emission reductions provided by these technologies can be realised today.
These possibilities are not just theoretical. Digital leaders in the industry are already using digital technologies, not only to reduce emissions but also to enhance operational efficiency, make data-driven decisions, innovate, and drive down operational costs. Their success stories serve as a powerful motivation for others to follow suit.
A key example is OYAK Cement, Turkey’s largest cement and concrete brand, which has embarked on a digital transformation journey centred on data infrastructure and cleansing. This has provided a solid foundation for layering AI optimisation on top, resulting in nearly 140,000 tons of CO2 reduction in a year.
After the completion of an upgrade of the digitalisation infrastructure of its plants, a leading cement producer in South America deployed our AI software sensor for free lime resulting in a 25% reduction in clinker quality variance and a tangible ROI in a year.
With so many opportunities to implement digitalisation – from deploying sensors and automation tools like DCS or SCADA to installing data historians and facilitating cloud‐based data access or leveraging AI and machine learning – there is plenty that the innovation ‘laggards’ in industry can do to catch up, and also pave the way for the technologies of the future. Our latest whitepaper – Digitalisation: The Pathway to Net Zero – highlights case studies of digitalisation from within the cement industry to derive key learnings, including opportunities and roadmaps for success, the pitfalls to avoid, and where to prioritise action – read it here.