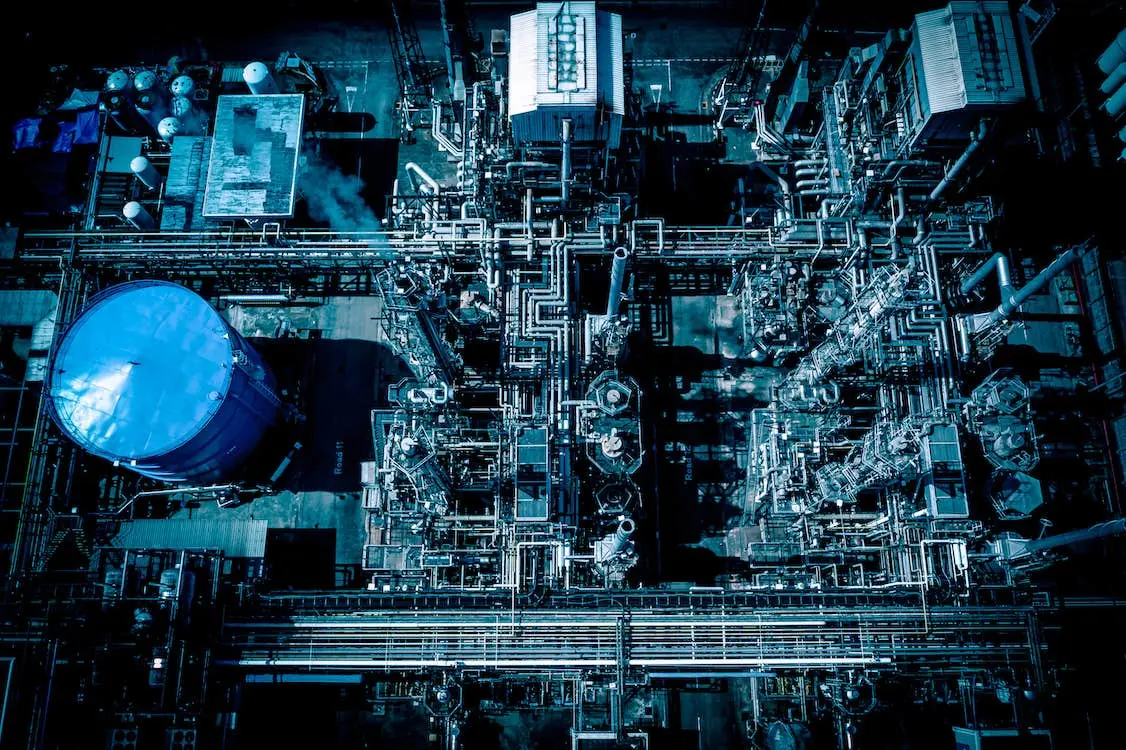
Digital technologies are transforming cement plants and paving the way for a more sustainable future. The industry is embracing digitalisation to turn the challenge of inefficiencies and high energy consumption into an opportunity to unlock new levels of product quality and productivity.
The need for digitalisation in cement plants
Cement production is an energy-intensive process across the entire production chain from raw material extraction, grinding and blending to kiln heating, clinker cooling, and cement milling. These operations require precise control of many interconnected variables to ensure optimal product quality while minimising resource consumption.
Traditionally, these processes have been managed manually, in some instances supported by basic automation systems. However, as this is a highly complex process, this manual intervention can lead to human errors and inconsistencies. Moreover, without real-time data monitoring and analysis capabilities provided by digital solutions, plant operators struggle to optimise performance let alone identify or deal with potential issues.
Digitalisation offers a solution by integrating various technologies such as the Industrial Internet of Things (IIoT) e.g. sensors, big data analytics, and cloud computing into existing cement plant infrastructure. These technologies allow for real-time monitoring of critical parameters across production while providing actionable insights for operational improvements. This technology also enables advanced Industry 4.0 capabilities such as AI, and machine learning, adding predictive capabilities. But what does this look like in practice?
The benefits of digitalisation
With the introduction of digitalisation infrastructure such as sensors and cloud historians, plant operators can monitor and store data in real-time. The data collected on variables like temperature profiles inside kilns or power consumption during grinding processes provides operators with a holistic view of their plant and begins to facilitate the identification of inefficiencies before they become costly problems.
Moreover, with AI and machine learning, a plant’s fuel consumption can be modelled and optimised to unlock previously out-of-reach efficiencies. For example, the AI models used by our product, can optimise kiln temperature profiles to reduce fuel consumption while maximising clinker quality. As fuel is one of the most significant cost factors for cement manufacturers this enables considerable reductions in operational expenses. Additionally, digital solutions enable intelligent power management systems that prioritise renewable energy sources like solar or wind power when available.
Consistency in product quality is crucial for cement manufacturers to meet customer expectations and with a digitalised cement plant, operators can make adjustments in real time to optimise the blending of raw materials or adjust quality indicators like CS3. This level of precision ensures that the final product meets desired specifications consistently.
Cement production involves potentially hazardous processes such as handling heavy machinery, high-temperature operations, and exposure to dust particles. While traditional safety measures were effective, digitalisation takes safety standards to a new level. Through IoT-enabled devices, sensors, and cameras, cement plants can identify potential safety hazards promptly. This proactive approach significantly reduces workplace accidents, making cement plants safer environments for employees.
Additionally, the integration of AI models enables predictive maintenance practices that help reduce downtime due to unexpected breakdowns. This results in improved overall equipment effectiveness and reduced maintenance costs.
Digitalisation is a significant, largely untapped opportunity to reduce emissions in the cement industry. Conventional cement manufacturing produces significant amounts of CO2, resulting from the calcination of limestone and the burning of fossil fuels. By optimising energy consumption, reducing waste, and integrating renewable energy sources, cement manufacturers can reduce their carbon footprint significantly. Real-time monitoring and analytics enable plant operators to track environmental data and make informed decisions to minimise their impact on the environment.
The future of cement plants lies in embracing digital technologies that unlock efficiency and productivity while promoting sustainability. By harnessing the power of IoT, AI, ML, big data analytics, and cloud computing, cement manufacturers can revolutionise their production processes and pave the way for a more sustainable future.